Marco Taisch (nella foto sopra), docente di Advanced e Sustainable Manufacturing presso il Dipartimento di Ingegneria Gestionale e Ingegneria Industriale del Politecnico di Milano e presidente di Made, il competence center del Polimi, è stato uno dei componenti della cabina di regia che ha contribuito alla stesura del Piano nazionale per l’Industria 4.0. A quattro anni di distanza dalla prima presentazione del Piano, è con lui che abbiamo fatto il punto sul cammino percorso finora dal nostro Paese per affrontare la quarta rivoluzione industriale e su ciò che va ancora fatto per completare la trasformazione digitale delle nostre imprese.
A partire dal 2016, quando è stato presentato il Piano Industria 4.0, il primo grande progetto per ridisegnare le politiche industriali del nostro Paese ha cambiato vari nomi e mutato – almeno parzialmente – “forma”. Qual è il suo giudizio sul cammino percorso finora?
Il Piano era partito molto bene, con una fortissima sponsorizzazione politica e un’intensa attività di comunicazione. Il ministro Calenda aveva investito sul Piano e si era speso in prima persona. Durante il primo Governo Conte l’impegno si è un po’ affievolito, ma con il ministro Patuanelli siamo tornati ad avere un presidio forte e lo si è visto con le modifiche migliorative che sono state attuate (ad esempio, il passaggio dal sistema dell’iper e super ammortamento al credito d’imposta).
Come giudica l’ultima versione del Piano, Transizione 4.0, che nelle intenzioni del Mise, tra le altre cose, doveva assicurare una politica industriale del Paese attenta alla sostenibilità?
Credo che sia fondamentale affiancare alla trasformazione digitale, quindi al 4.0, i temi della sostenibilità, del Green New Deal perché questo vuol dire aver finalmente compreso che questi due trend, tecnologici da un lato di business dall’altro, si rafforzano a vicenda. Per operare in modo sostenibile posso lavorare sui materiali, sull’economia circolare, ma la digitalizzazione è il backbone perché tutto questo avvenga. La digitalizzazione mi consente di raccogliere dati, di prendere informazioni e quindi di condurre impianti e di realizzare prodotti in maniera tale che il comportamento d’uso sia più sostenibile. Se la mia auto mi evidenzia quanto carburante spreco facendo brusche accelerate, alla fine sono indotto a cambiare la mia modalità di guida per consumare meno.
Il ministro Patuanelli ha annunciato un potenziamento del Piano Transizione 4.0 e un Piano Impresa 4.0 Plus, la misura allo studio del Governo che è stata annunciata nel documento Progettiamo il Rilancio e che intende incentivare gli investimenti nelle “tecnologie di frontiera” come la Blockchain, il Quantum Computing e l’Intelligenza Artificiale. Come giudica quanto è emerso finora su queste due misure?
Mi sembra che si vada nella direzione corretta quando si annuncia un raddoppio delle aliquote e, soprattutto, una stabilizzazione del Piano per tre anni che darebbe certezza alle imprese aumentando la loro capacità di pianificazione degli investimenti. Gli investimenti nell’Industria 4.0, infatti, hanno bisogno di una pianificazione di medio-lungo periodo, quindi le imprese non possono vivere nell’incertezza senza sapere se l’anno successivo gli incentivi saranno rinnovati. Solo con la stabilità le imprese possono investire sulle tecnologie 4.0
L’ultima versione del Piano pone maggiore attenzione all’inclusività, al coinvolgimento delle piccole e medie imprese che costituiscono l’ossatura del nostro sistema imprenditoriale e sembravano essere rimaste ai margini delle prime versioni del Piano.
Io su questo ho un’opinione diversa, nel senso che il Piano Industria 4.0 era già inclusivo, non c’era un limite verso il basso degli investimenti: si potevano investire solo 5.000 euro e si otteneva l’iperammortamento su 5000 euro. Non è vero che il Piano Nazionale Industria 4.0 del 2017 non fosse pensato anche per le piccole e medie imprese. Le PMI non l’hanno utilizzato perché, quando il Piano è stato presentato, molte di loro hanno sentito parlare di 4.0 per la prima volta. Da due anni a questa parte le PMI hanno avuto modo di informarsi e adesso hanno capito cos’è l’Industria 4.0, cos’è la trasformazione digitale. Quando è stato presentato il Piano Industria 4.0, c’era una sacca significativamente ampia di aziende, per lo più piccole e medie, che non avevano le risorse di know-how per rimanere sulla frontiera dell’innovazione tecnologica. Queste imprese hanno beneficiato del Piano non fruendo dell’iperammortamento, ma accrescendo la propria awareness, la propria consapevolezza dell’importanza della quarta rivoluzione industriale. Grazie alla presenza di incentivi fiscali, quelle aziende inizialmente poco consapevoli hanno partecipato a convegni, si sono informate, hanno capito cos’è l’Industria 4.0 e adesso sono pronte ad affrontarla. Le grandi imprese, invece, erano già pronte ad utilizzare le misure fiscali del Piano Industria 4.0 perché già nel 2015-2016 avevano avuto la possibilità di affrontare i temi dell’Industria 4.0. Se hanno usufruito dell’iperammortamento prevalentemente le grandi imprese, dunque, non è stato perché il Piano non fosse aperto alle PMI, ma per la mancanza di consapevolezza da parte di molte di esse.
Il nostro Paese, partito in ritardo sulla strada della quarta rivoluzione industriale, ha recuperato posizioni, o il gap con gli altri Paesi industrializzati è ancora significativo?
Diciamo che stiamo seguendo lo stesso trend degli altri Paesi industrializzati. Abbiamo fatto bene a lanciare il Piano Industria 4.0 che ha evitato l’aumento del gap di produttività che abbiamo rispetto agli altri Paesi con i quali normalmente ci confrontiamo. Però tale gap non l’abbiamo recuperato, stiamo solo viaggiando alla stessa velocità degli altri. Il Covid-19, poi, ha ovviamente peggiorato la situazione.
In che modo, a prescindere dagli incentivi fiscali, le aziende e le organizzazioni che non hanno ancora un livello di innovazione avanzato possono cogliere le opportunità offerte dalle tecnologie della quarta rivoluzione industriale?
Innanzitutto bisognerebbe mettere da parte paure e scetticismo, frutto dell’ignoranza dei vantaggi che può portare l’Industria 4.0. Molte persone, vuoi per l’età, vuoi per la mancanza di competenze digitali (non dimentichiamoci che l’Indice di digitalizzazione dell’economia e della società (DESI) vede l’Italia al terz’ultimo posto e le maggiori carenze riguardano proprio il capitale umano), stentano a comprendere le tecnologie dell’Industria 4.0 e, non riuscendoci, voltano la testa dall’altra parte e continuano per la propria strada. Bisogna, invece, avere l’umiltà di cercare di capire cos’è l’Industria 4.0 e non avere paura degli investimenti necessari per affrontarla. Non stiamo parlando, infatti, dei grandi investimenti per i sistemi informativi aziendali (ERP) affrontati dalle aziende tra il 2000 e il 2005, impegnativi sia dal punto di vista del budget sia dal punto di vista dell’organizzazione aziendale. La connessione di una macchina in fabbrica non richiede la trasformazione della propria organizzazione, ma si affianca ad essa: si apre un canale di comunicazione tra un pc e la macchina, ma si può continuare a lavorare come prima. L’impatto sull’organizzazione non c’è o è molto tenue, non è invasivo né pervasivo. L’operazione può essere fatta “a macchia di leopardo”: si connette una macchina, si cominciano a capire i vantaggi, poi si connette una seconda macchina e poi una terza, non si devono connettere tutte insieme. La gradualità insita nelle tecnologie 4.0 deve rassicurare, eliminando meccanismi di rifiuto e di rigetto dell’innovazione.
Lei mette l’accento sulla necessità di digitalizzare le nostre imprese. Spesso, però, è più facile misurare l’investimento in un nuovo macchinario piuttosto che in un nuovo software.
Il software non “produce pezzi” e, quindi, è più difficile avere delle evidenze tangibili. La verità, comunque, è che dobbiamo smetterla di considerare le risorse spese in digitalizzazione come un investimento: in realtà sono un prerequisito di business, così come un tempo lo era l’acquisto di un fax o di un telefono. Se non destiniamo delle risorse alla digitalizzazione, altri lo faranno e alla fine dell’anno avranno un conto economico più alto, mentre noi entro tre anni saremo fuori dal mercato.
Secondo uno studio dell’Osservatorio School of Management del Polimi l’organizzazione dei progetti 4.0 è ancora una lacuna per molte aziende italiane. A cosa è dovuta, secondo lei, questa difficoltà delle nostre imprese a seguire un programma strutturato nell’implementazione delle tecnologie dell’Industria 4.0?
Una parte di colpa ce l’hanno le imprese, ma c’è anche il problema che oggi l’Industria 4.0 è monopolizzata da chi ha competenze prettamente informatiche (parlo dei fornitori), ma senza la capacità di gestire grandi progetti. Molti pensano di andare in azienda, installare una macchina e il relativo software e di aver così concluso il progetto. Per supplire a queste mancanze è importantissima l’attività dei Competence Center, nati proprio per aiutare le imprese a sviluppare la cultura del progetto. I Competence Center non vendono software, però aiutano nella gestione e nella comprensione del progetto e, soprattutto, nella valorizzazione dei benefici.
Nell’emergenza sanitaria le tecnologie digitali sono diventate strumenti per reagire alla crisi. Ma aiutano anche a comprendere le direzioni dell’Industria 4.0 nella nuova normalità. Su quali tecnologie digitali ci conviene puntare nel prossimo futuro, in quella che è stata definita l’era del New Normal?
Secondo me conviene puntare ancora sull’Industrial IoT. Oggi è più di moda parlare di Intelligenza Artificiale e di Blockchain e, pensando al medio e lungo periodo, queste saranno tecnologie fondamentali in futuro ed è giusto che il Paese abbia la sua Agenda per l’Intelligenza Artificiale e che investa in attività di ricerca e innovazione. Non dimentichiamoci, però, che una cosa è l’attività di ricerca e innovazione, un’altra cosa è la maturità di una tecnologia e la capacità del sistema industriale di utilizzare tale tecnologia. Le nostre imprese hanno ancora una troppo scarsa maturità digitale per poter utilizzare l’Intelligenza Artificiale. È meglio che prima comincino a connettere le macchine apprendendo a leggerne i dati, a fare monitoraggio da remoto. Guidiamo le nostre automobili leggendo sul cruscotto in maniera assolutamente naturale decine di indicatori sullo stato della vettura mentre non lo facciamo su una macchina utensile, su un impianto che produce valore aggiunto per centinaia di migliaia di euro nell’unità di tempo. Leggere le prestazioni del proprio impianto produttivo, chiedersi, ad esempio, come si può portare l’efficienza dal 70 all’80%, magari con interventi minimi: è così che si recupera produttività nell’azienda e poi nel Paese. L’IIoT, il monitoraggio remoto, la connessione delle macchine, è su questo che dobbiamo puntare e infatti sono tecnologie ancora incentivate nel Piano nazionale. Poi certo bisogna lavorare in maniera ancora più seria sull’Additive Manufacturing, sull’Intelligenza Artificiale, tecnologie che non possiamo certo trascurare.
L’interconnessione dei macchinari, il primo passo per la digitalizzazione del processo produttivo, potrebbe avere come conseguenza il cambiamento dei modelli di business delle nostre imprese.
Esatto. Dopo il Covid tutti quei modelli di business che già conoscevamo, ma che non venivano implementati ed erano snobbati per pigrizia, per ignoranza, diventeranno fondamentali. Il monitoraggio da remoto, la manutenzione da remoto, i collaudi in remoto, sono tutti modelli di business che possiamo utilizzare per creare nuovi servizi, nuovo margine. Oggi le aziende hanno personale interno che si occupa di pianificazione della produzione, perché è necessaria la presenza in fabbrica. Domani, se tutte le macchine saranno connesse, i dati delle stesse (quello che stanno facendo, il piano di produzione), con le tecnologie che attualmente sono a disposizione, potranno essere a disposizione di una persona che si trova a centinaia di chilometri di distanza. Quella persona potrà benissimo fare da remoto la pianificazione della produzione, senza bisogno di essere presente in fabbrica. L’operatore da remoto, che fa tutto il giorno pianificazione della produzione, sarà sicuramente molto più bravo del capo reparto o dell’ingegnere di produzione che, oltre a quell’attività, fanno anche mille altre cose. Pagando un servizio da remoto, è possibile concentrare un’attività, quella della pianificazione della produzione, in una persona che probabilmente la farà meglio di tutti, garantendo, così, un piano di produzione più efficiente. Ecco che nasce un nuovo business.
Adesso che abbiamo individuato le tecnologie sulle quali puntare nel prossimo futuro, vorrei capire quali sono le competenze sulle quali occorrerà investire per affrontare l’epoca del New Normal.
Dobbiamo investire sulle competenze necessarie per governare le tecnologie di cui ho parlato prima, in particolare la capacità di leggere e utilizzare i dati forniti dall’IIoT. C’è bisogno di un mindset, di un atteggiamento mentale per cui si parte dai numeri per scegliere quali azioni intraprendere. Le decisioni devono essere basate sui dati, sulla consapevolezza quantitativa e non sulle sensazioni. Anche i blue collar, gli operatori, oltre alle competenze specifiche che gli consentono di svolgere le solite attività, dal caricare una macchina utensile al programmare il PLC, dovrebbero avere un minimo di competenze di ingegneria industriale. In fabbrica dobbiamo sensibilizzare all’utilizzo degli indicatori di misura delle prestazioni, che oggi in molti casi manca. Quando vado in azienda vedo ancora troppe decisioni basate su sensazioni, non sui numeri.
Se è vero – come dice Klaus Schwab, fondatore del World Economic Forum di Davos – che per affrontare la quarta rivoluzione industriale è fondamentale “apprendere attraverso la pratica e investire nelle persone”, è stato fatto abbastanza finora per ridurre il mismatch qualitativo e quantitativo tra domanda e offerta di lavoro?
No e imprese e lavoratori sono corresponsabili di questo. Le imprese hanno ritenuto e ritengono ancora oggi la formazione una cosa non rilevante e ciò è frutto di un atteggiamento miope e dell’incapacità di guardare lontano dell’imprenditore, del manager. Dall’altra parte, però, c’è una responsabilità del lavoratore e dei sindacati che vedono la formazione come un diritto e non come un dovere. La provocazione che ho lanciato al World Manufacturing Forum dell’anno scorso è proprio questa: il lavoratore deve smettere di vedere la formazione come un diritto, qualcosa che “deve” fare nelle ore previste dal contratto (otto ore di formazione in un anno, tra l’altro, non sono nulla) e per la quale deve essere pagato. Il lavoratore dovrebbe capire che mantenersi aggiornato è una sua responsabilità perché ne va della sua professionalità. Se non si fa nulla per rimanere aggiornati, competitivi, per avere un valore nel mondo, poi non ci si può lamentare se dopo 20 anni nel mondo del lavoro non si trova più un’occupazione. Il mondo andrà sempre avanti, non ci si può lamentare di questo e allora, come si fa il revamping (ammodernamento, ndr) delle macchine, le persone dovrebbero fare il proprio auto-revamping.
Il ministro Patuanelli ha detto che il Credito d’imposta formazione 4.0 “non ha funzionato proprio per niente”. Condivide anche lei questo giudizio così negativo?
Non ha funzionato perché prevede la contrattazione di primo e secondo livello che blocca tutto. L’iperammortamento ha funzionato perché non c’era nulla da fare: cambiava solo l’aliquota, non c’era bisogno di chiedere permessi, pre-autorizzazioni, non si doveva negoziare con i sindacati. Se avessi bisogno di fare formazione per cinque persone, passerei più tempo a negoziare che a erogare formazione. Il fatto, poi, che venga pagato il costo del lavoro delle ore di formazione penalizza le piccole aziende che faticano a coprire i costi della docenza avendo poche persone da formare, mentre rende l’incentivo più appealing per le grandi imprese che possono formare aule con molte persone.
Il “Fondo Nuove Competenze” (art. 88 del Decreto Rilancio) potrebbe rappresentare un’altra opportunità per le aziende desiderose di accrescere le competenze dei propri dipendenti. Lei cosa ne pensa?
Potrebbe essere la strada giusta da seguire. Invece di creare nuovi strumenti, comunque, a volte basterebbe semplificare quelli che ci sono già.
Per i prossimi mesi, dunque, su cosa dovrebbero puntare le nostre imprese per essere più resilienti e superare questa crisi?
Dovrebbero puntare sulla formazione e avere il coraggio di investire. Uno dei miei professori mi diceva sempre che bisogna investire nei momenti di crisi. Se si investe nei momenti in cui l’economia va bene è già troppo tardi. È chiaro che c’è una crisi di liquidità, ma arriveranno tantissimi soldi, usiamoli bene. È un’occasione irripetibile quella che abbiamo davanti, non possiamo farcela scappare.
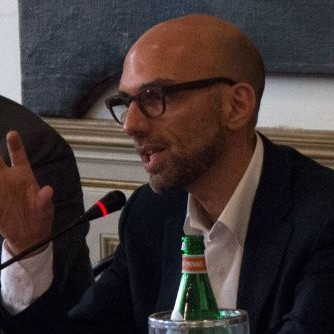
Direttore responsabile de Il Giornale delle PMI