L’economia globale mostra come grandi aziende internazionali abbiano affrontato con metodi strutturati e risolto con successo problemi di produzione, e ottenendo notevoli miglioramenti di impatto sul mercato. Toyota ha implementato il sistema di produzione Just-In-Time, riducendo i tempi di ciclo del 50% e aumentando l’efficienza operativa del 30%. Anche General Electric ha adottato il programma Six Sigma, che ha portato a una riduzione del 40% nei difetti di produzione e a risparmi annuali di circa 1 miliardo di dollari.
L’adozione di approcci strutturati al problem solving e la pratica di programmi di miglioramento continuo possono portare a notevoli benefici in termini di produttività, efficienza e qualità nel settore metalmeccanico. La stessa Caterpillar ha migliorato la produttività del 25% e ridotto i costi operativi del 15% grazie all’implementazione del Lean Manufacturing.
Secondo uno studio della McKinsey, le aziende che adottano tecniche di miglioramento continuo registrano un incremento medio della produttività del 20% e una riduzione dei costi di produzione del 15%
E nelle nostre PMI?
Chi guida una società metalmeccanica può seguire il metodo degli otto passi del problem solving
Identifica il problema: Ad esempio: Ci sono cali di produttività nei reparti, che causano ritardi nelle consegne e insoddisfazione tra i clienti.
- Attività: Definisci chiaramente il problema come “calo della produttività”, identifica i sintomi in modo specifico: ritardi nelle consegne, aumento degli scarti di produzione e feedback negativo dai clienti. Ad esempio, un ritardo del 10% nei tempi di consegna rispetto al trimestre precedente.
2. Acquisisci i dati: Raccogli informazioni attendibili, cioè numeri, sulla produttività e sulle operazioni della fabbrica.
- Attività: Analizza i dati di produzione, raccogli feedback dagli operai e dai capi reparto, esamina i rapporti di qualità e gli inventari, e confronta le performance attuali con i dati storici e i benchmark del settore. Ad esempio, raccogli i dati giornalieri sulla produzione per identificare fluttuazioni.
3. Analizza i dati: Esamina i dati per identificare le cause del calo di produttività.
- Attività: Utilizza strumenti come l’analisi delle cause alla radice, crea diagrammi di flusso per mappare il processo produttivo, identifica colli di bottiglia e inefficienze, e valuta l’impatto di eventuali cambiamenti recenti nelle operazioni. Un’analisi potrebbe rivelare che il 20% del calo di produttività è dovuto a macchinari obsoleti.
4. Genera una molteplicità di soluzioni: Sviluppa diverse strategie per migliorare la produttività.
- Attività: Organizza sessioni di brainstorming con i capi reparto e gli operai, proponi soluzioni come l’ottimizzazione dei processi produttivi, introduci nuove tecnologie o attrezzature, rendi costante la formazione del personale e il miglioramento della manutenzione preventiva. Ad esempio, considera l’acquisto di nuove macchine CNC per aumentare la precisione e la velocità di produzione.
5. Decidi la soluzione: Scegli la soluzione più efficace per aumentare la produttività.
- Attività: Valuta le varie soluzioni in base ai costi, benefici, fattibilità e impatto a lungo termine; coinvolgi i diretti interessati nella decisione finale e attua il programma di ottimizzazione dei processi combinato con la formazione del personale. Un esempio potrebbe essere scegliere una nuova soluzione tecnologica che prevede un investimento iniziale di 50.000 euro con un ritorno previsto del 15% annuo in termini di produttività aumentata.
6. Implementa la soluzione: Metti in pratica le soluzioni scelte per migliorare la produttività.
- Attività: Sviluppa un piano dettagliato per l’ottimizzazione dei processi, programma sessioni di formazione per il personale, aggiorna le attrezzature e i macchinari se necessario, e comunica i cambiamenti al team. Ad esempio, metti in opera un nuovo sistema di gestione della produzione entro sei mesi.
7. Valuta l’impatto dell’implementazione: Monitora i risultati delle nuove iniziative di produttività.
- Attività: Raccogli i dati sulla produttività dopo l’attuazione delle nuove soluzioni, confronta i risultati con gli obiettivi stabiliti, raccogli feedback dal personale e dai clienti, e identifica eventuali problemi o necessità di ulteriori aggiustamenti. Ad esempio, monitora se l’aumento della produttività del 15% nei primi tre mesi dopo l’implementazione si è verificato.
8. Continua a migliorare: Adotta un approccio di miglioramento continuo per ottimizzare la produttività.
- Attività: Conduci revisioni periodiche del processo produttivo, raccogli e analizza continuamente i feedback del personale e dei clienti, apporta modifiche basate sui dati raccolti, e promuovi una cultura aziendale orientata al miglioramento continuo dell’efficienza e della qualità della produzione. Ad esempio, stabilisci revisioni trimestrali dei processi produttivi per identificare ulteriori opportunità di miglioramento.
Questi otto passi possono aiutare una PMI del settore metalmeccanico a migliorare produttività, efficienza e qualità complessiva, contribuendo così a una maggiore competitività sul mercato.
Fondamentale agire con metodo e con un preciso piano di lavoro. Fallo con le tue persone, sia con i tuoi riporti diretti che con gli operatori più vicini all’azione.
La frase su cui riflettere
“Un obiettivo senza un piano è solo un desiderio”, Antoine de Saint-Exupéry.
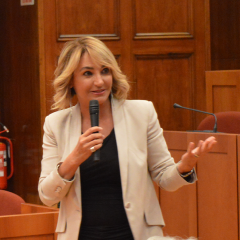