L’adozione delle nuove tecnologie digitali sta cambiando i processi e i modelli di business in diversi settori. Fino a qualche anno fa, la portata del cambiamento determinato dall’applicazione dell’intelligenza artificiale era impensabile. Oggi invece, sta crescendo la consapevolezza dell’importanza di attuare una rivoluzione che per molti aspetti appare necessaria, da un lato per garantire una crescita sostenibile nel lungo periodo, dall’altro per rimanere competitivi e non essere sopraffatti da coloro che hanno già intrapreso il percorso verso l’intelligenza artificiale. Il Digital Twin si inserisce in questo contesto diventando fondamentale nei processi di innovazione, soprattutto grazie alla capacità di monitorare, analizzare e prevedere la realtà esterna.
È una tecnologia emergente destinata a cambiare e trasformare lo scenario di molti settori, è un fattore importante per realizzare la trasformazione digitale. Le applicazioni sono infatti ad ampio raggio: dal settore aerospaziale (dove è stato applicato per la prima volta) all’ambiente industriale, alla gestione di edifici o di città fino all’analisi dei comportamenti delle persone.
Esaminiamo di seguito cosa sia e quale portata ha per l’industria.
Che cos’è il Digital Twin?
L’attuale concetto di Digital Twin può essere fatto risalire al 2002, quando il Dr. Michael Grievs, presso l’Università del Michigan, durante il Product Lifecycle Management (PLM) descrisse il tutto come un’immagine speculare (o un gemello) di ciò che esiste nel mondo reale e virtuale. Da allora, la terminologia è cambiata ma il suo significato è rimasto abbastanza stabile. Si basa sull’idea che un sistema fisico possa essere ricreato digitalmente attraverso le informazioni e le logiche che caratterizzano il sistema fisico stesso. Il sistema fisico e il sistema digitale sono strettamente integrati durante tutto il ciclo di vita e si sviluppano insieme. Le informazioni elaborate dalla copia digitale si configurano come “gemelle” delle informazioni del sistema fisico. Il vantaggio è che, in condizioni ideali, qualsiasi informazione che si possa ottenere dall’analisi di un bene o da un processo reale possa essere ottenuta attraverso l’interrogazione del suo gemello digitale. “Pertanto, il Digital Twin è definito come un insieme di informazioni virtuali che descrivono completamente un prodotto fisico, un sistema o un processo, in modo da poter valutare il suo stato o il funzionamento attuale e futuro”.
Una definizione di questa nuova dinamica l’ha data Robert Plana, Innovation & Ecosystem Director di GE Digital, società del gruppo General Electric che sviluppa soluzioni per IIoT, che così la descrive: «Il digital twin è una sorta di modello in vivo di un impianto o di una linea di produzione, realizzato dall’incrocio tra i dati reali di funzionamento e i disegni cad e digitali serviti per la progettazione. Il digital twin consente di costruire una copia virtuale dell’impianto reale, ma anche di una singola macchina, in grado di replicare in tutto e per tutto il funzionamento reale o di verificarne tutte le possibili alternative».
Ciò che rende esclusivo il Digital Twin è dunque la sua capacità di fornire informazioni sullo stato attuale, le prestazioni e la salute delle risorse e dei processi tanto quanto simulare opzioni future per ottimizzare attività e servizi. Un esempio? Se un manager vorrà apportare una qualsiasi variazione di una procedura, potrà testare la stessa, senza rischi, nell’ambiente digitale, ottenendo informazioni assolutamente reali. Allo stesso modo, monitorando lo stato del sistema reale a livello digitale, potrà accadere di scoprire in anticipo una potenziale criticità, potendo così apportare le adeguate contromisure per prevenire un possibile problema in futuro. In un mercato competitivo, il valore dell’informazione è essenziale e arrivare per primi per sapere cosa succederà domani è l’ambizione di ogni imprenditore che così potrebbe raggiungere più facilmente gli obiettivi.
Il cuore tecnologico del Digital Twin
Gli ultimi sviluppi nella digitalizzazione hanno notevolmente migliorato le capacità di raccolta dei dati. Da un lato, questa svolta ha contribuito a colmare le lacune informative necessarie per risolvere i principali problemi aziendali, dall’altro ha anche portato nuove sfide legate alla necessità di estrarre valore potenziale dai dati stessi. L’Industria 4.0 racchiude la digitalizzazione e promuove la visione di una fabbrica interconnessa dove strutture, macchinari e oggetti sono online, intelligenti e capaci di collaborare in modo integrato. Questo nuovo paradigma descrive ampiamente un ambiente digitale che raccoglie e unisce dati da diverse fonti per creare un’impresa coordinata in grado di comunicare, analizzare e utilizzare queste informazioni per veicolare ulteriori azioni “intelligenti” nel mondo reale.
Digital Twin è la naturale realizzazione di questa visione e influisce sull’ecosistema aziendale in molteplici modi: tecnologia, informazione, processi e competitività aziendale. Molte aziende hanno già adottato strategie di ecosistema di business digitale con applicazioni Digital Twin di diverse scale e, che lo sappiano o meno, hanno creato il know-how, il software e l’infrastruttura hardware per implementare la strategia.
Ogni Digital Twin è composto da un software che esegue modelli interconnessi con i dati in tempo reale da linee di produzione, personale e magazzini. Questo Digital Twin può inviare i propri dati di controllo ed eventuali anomalie ad un applicativo di visualizzazione costituito da un cruscotto su PC, tablet o smartphone secondo necessità. Insieme ai dati di monitoraggio in tempo reale e alle notifiche istantanee di allarme, Digital Twin visualizzerà tutti gli “eventi futuri” che si prevede possano verificarsi a breve, medio e medio-lungo termine. Il modello è in grado di auto-allenarsi e adattarsi ai cambiamenti delle impostazioni aziendali senza una riconfigurazione del sistema.
L’Internet of Things, è la chiave di questa tecnologia. L’aumento dell’accessibilità dei sensori, l’uso ormai diffuso del Wi-Fi e la capacità di trasmissione dei dati del cloud si combinano per rendere le applicazioni di modellazione digitale accessibile su larga scala rendendole adatte a varie soluzioni e a una ampia platea di aziende.
Digital Twin nell’Industria Manifatturiera
Il Manifatturiero è uno dei diversi ambiti in cui il Digital Twin trova applicazione.
Questo utilizzo influenzerà significativamente la progettazione, la produzione e la manutenzione del prodotto, rendendo così la produzione più efficiente ed efficace.
Attraverso il processo di digitalizzazione tipo top down, il prodotto nasce prima virtualmente e poi viene materializzato. In altre parole, il Digital Twin consente una pianificazione virtuale strategica di prodotti e processi: utilizzare strumenti di simulazione per elaborare, analizzare e valutare grandi quantità di dati in modo che possano essere forniti in tempo reale per prendere decisioni efficaci. Il Digital Twin sta diventando un imperativo aziendale che copre l’intero ciclo di vita di un bene o di un processo e costituiscono la base per prodotti e servizi interconnessi.
L’impatto della tecnologia Digital Twin può essere suddiviso in 3 “zone” principali:
- Produzione & Progettazione
- Prodotti in produzione
- Prodotti futuri
Produzione & Progettazione
Il Digital Twin industriale ottimizza l’efficienza prevedendo i guasti di produzione in modo che possano essere riparati prima che influiscano sugli obiettivi di produzione. I miglioramenti stessi possono essere simulati regolando i parametri lungo la linea di produzione gemella senza rischiare danni alla produzione. Le Simulazioni riuscite possono essere applicate al sistema effettivo.
Inoltre, il team di ingegneri può analizzare il Digital Twin dei prodotti per confrontare le prestazioni effettive del prodotto con le prestazioni attese durante la fase di progettazione. Le deviazioni comportamentali possono essere valutate per influenzare le future iterazioni di sviluppo del prodotto.
Prodotti in produzione
Il sistema Digital Twin industriale consente il debug e la diagnosi a distanza di prodotti esistenti in loco, riducendo i costi di servizio e aumentando la soddisfazione del cliente.
Se un tecnico deve interagire fisicamente con il prodotto per risolvere il guasto, il problema può essere diagnosticato a distanza tramite Digital Twin per ordinare le apparecchiature e le parti necessarie. Allo stesso modo, quando un nuovo prodotto deve essere affidato ai clienti, può essere configurato dal personale di assistenza remota.
Prodotti futuri
Nuovi prodotti possono essere sviluppati comprendendo il comportamento dei prodotti esistenti nel mondo reale. Le prestazioni e l’utilizzo dei clienti vengono proiettate nel gemello digitale, che quindi influenza lo sviluppo del prodotto e il suo processo di produzione per aumentare i profitti, la soddisfazione del cliente e il mercato.
I benefici e il valore aggiunto della tecnologia Digital Twin
I benefici e i vantaggi di un Digital Twin sono nascosti all’interno del suo stesso nome: una copia digitale della realtà, in cui “vedere”, “pensare” e “agire”, è completamente privo di rischi. Il concetto di Digital Twin ha un grande potenziale e si realizza nei seguenti modi:
Miglioramento continuo il coinvolgimento nel Digital Twin di molte altre tecnologie digitali e innovazioni è la chiave di volta che determina inevitabilmente futuri miglioramenti aziendali.
Predittività il Digital Twin può essere utilizzato per prevedere lo stato futuro delle risorse aziendali e l’impatto di eventuali problemi chiavi (ad esempio, interruzioni di servizio o malfunzionamenti di vario genere) grazie all’utilizzo di diverse tecniche di modellazione (matematica o basata su simulazione o, ancora, su dati, etc.)
Analisi di scenario (what-if) interfacce utente correttamente progettate possono facilmente interagire con il sistema Digital Twin e testare diversi scenari per identificare le migliori azioni da implementare nel sistema reale.
Visibilità il Digital Twin può aumentare la visibilità delle operazioni delle macchine o di altri asset aziendali, nonché di più grandi sistemi interconnessi come impianti di produzione o aeroporti.
Conoscenza il Digital Twin può essere utilizzato come strumento di comunicazione e documentazione, per comprendere e spiegare i comportamenti di uno o più sistemi.
l’integrazione del sistema se è progettata correttamente, il Digital Twin può essere collegato ad altre applicazioni aziendali per estrarre i dati necessari per le sue operazioni, in particolare nelle operazioni della catena di fornitura (tra cui produzione, approvvigionamento, gestione del magazzino, trasporto e logistica, assistenza in loco, ecc.
Modello dirompente di business il Digital Twin non solo migliora i modelli di business tradizionali, ma ne abilita anche di nuovi, come quelli basati su concetti di “servitizzazione” che contiene conoscenze sulla salute degli asset e piani di attività corretti per garantire servizi adeguati.
Adottare il Digital Twin nel mondo industriale significa anche:
- capacità di risolvere problemi comuni in anticipo prima del lancio dei prodotti sul mercato;
- riduzione dei difetti del prodotto e dei costi di produzione per eliminare quasi tutti i rischi nei prodotti futuri;
- trasferire il processo di verifica nel mondo virtuale mantenendo comunque la connessione fisica-virtuale consentendo di analizzare le prestazioni di un prodotto in varie condizioni e apportare le modifiche necessarie nel mondo virtuale per garantire che le prestazioni del prodotto soddisfino pienamente le aspettative;
- verifica del processo di produzione, che funziona prima della produzione effettiva. Migliorando questa funzione, l’azienda può prevenire costosi tempi di fermo macchina e robot in fabbrica. È inoltre possibile prevedere quando è necessaria la manutenzione preventiva per evitare tempi di fermo non necessari;
- abbreviare il time-to-market: arrivare sul mercato più velocemente dei concorrenti è un problema che tutte le aziende devono affrontare;
- risparmio di tempo e denaro nella simulazione, test e analisi;
- affidamento non solo sul fisico: si possono includere informazioni dalle loro prestazioni fisiche nei gemelli digitali per mantenere una versione fedele del mondo virtuale.
Informazioni accurate e aggiornate forniscono l’intelligenza necessaria per prendere decisioni più rapide, aumentare la velocità di produzione e ottimizzare la produttività, ed entrare nel mercato più velocemente.
Le simulazioni preliminari, l’ausilio di copie virtuali di prodotti reali, ridurranno nel tempo i costi dei reparti di ricerca, grazie alle migliori condizioni di lavoro, ai consumi di prova e alle caratteristiche quantitative e qualitative dell’oggetto; al tempo stesso, aumenteranno anche le possibilità di effettuare modifiche anche minime ai processi. La simulazione offline dei robot consente, ad esempio, di controllare con precisione l’evoluzione dei pezzi lavorati dalla macchina, il che può ridurre completamente il verificarsi di anomalie di fabbricazione, garantendo così che i risultati siano il più vicino possibile alla perfezione. Del resto in un’azienda che oggi lavora con sistemi IoT, in cui ogni macchina è interconnessa con l’altra, i processi decisionali devono essere altrettanto istantanei.
E se, invece di replicare i meccanismi di una macchina o di un processo aziendale, fosse possibile replicare addirittura il comportamento degli individui?
Tra le potenzialità del “gemello virtuale”, possiamo annoverare anche il miglioramento nella gestione dell’esperienza del consumatore diventando vantaggioso e di aiuto per una campagna marketing: con la sua attuazione si interpretano meglio i bisogni degli acquirenti e, sulla base delle loro esperienze, possono essere sviluppate in tempi record le migliori evoluzioni dei prodotti esistenti.
L’analisi di macro-comportamenti degli individui (indipendentemente dai loro dati) consente di replicare in un ambiente Digital Twin le condiziono che hanno portato un soggetto potenzialmente interessato a un acquisto a diventare un cliente che ha effettivamente speso. Quindi, replicando le condizioni, inserendo diverse varianti, si può cercare di capire quale impatto avrà una campagna marketing e come cambierà l’elasticità della domanda di un dato cluster di clienti in certe situazioni, anche temporali. Anche in questo caso, il Digital Twin che non intende sostituirsi al marketing aziendale, fornirà suggerimenti basati sui di dati dinamici testati.
Molto semplicemente, la tecnologia del gemello digitale può fornire una vasta gamma di informazioni chiave che possono aiutare a guidare vendite, prevedere le tendenze e determinare le preferenze dei consumatori.
Le 5 sfide del Digital Twin
Di fronte ai tanti vantaggi e opportunità che l’introduzione di questa tecnologia può portare all’azienda, sono tante le sfide da superare:
- Connettività, che deve essere veloce, garantita e disponibile nelle diverse aree in cui si trova l’azienda per avere l’opportunità di interagire con il “gemello digitale” e prendere decisioni in tempo reale. Una condizione infrastrutturale purtroppo ancora non scontata in molte realtà italiane
- Hardware, ovvero potenza per poter consentire l’elaborazione in tempo reale dei dati a disposizione e per poter gestire in modo efficiente la sensoristica connessa essenziale al Digital Twin
- Lunghi cicli di vita, cioè progettare il gemello digitale tenendo conto del fatto che molti asset per i quali viene impiegata questa tecnologia sono caratterizzati da un lungo ciclo di vita, che generalmente si estende ben oltre la validità dei software proprietari utilizzati per il loro design, simulazione o analytics. Questo porta a considerare come un fattore di successo la selezione delle tecnologie da utilizzare, tenendo conto della loro obsolescenza
- Risorse umane, sono anche il cuore del Digital Twin e le loro competenze possono essere utilizzate per lo sviluppo e la gestione di questa tecnologia
- Sicurezza, viene messa in discussione e pone una sfida al Digital Twin, perché il gemello digitale accumula essenzialmente dati, capitale intellettuale e quindi crea valore per l’azienda, e ciò deve necessariamente essere protetto per evitare danni all’azienda.
In sintesi, possiamo dire che il Digital Twin è un metodo rivoluzionario, grazie al quale le aziende possono analizzare e ottimizzare le prestazioni di prodotti e processi nelle condizioni operative reali e fare previsioni affidabili sulle prestazioni future, migliorando l’efficienza operativa, la produttività, riducendo i costi e scongiurando il rischio di tempi di inattività non pianificati. In questo senso, si può certamente affermare che il Digital Twin sia una porta verso il futuro, nonché un motore quanto mai concreto per l’innovazione.
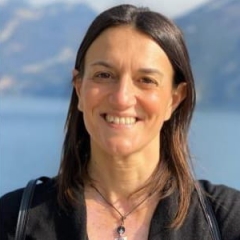
Laureata in Giurisprudenza, dopo aver maturato una significativa esperienza in ambito giuridico-legale, da qualche anno si è avvicinata al mondo della finanza agevolata, contributi a fondo perduto, industry 4.0 e innovazione.